- Simulate to predict
- Test to validate
- Measure to monitor
To ensure a service of the highest quality, V2i offer complementary services and tools:
- software tools enabling the correlation between experimental and predicted results. For example, V2i has developed specific tools dedicated to the dynamic analysis of cyclically repeating structures;
- instrumentation services to get additional information during a test;
- specific hardware and software tools for on-site troubleshooting.
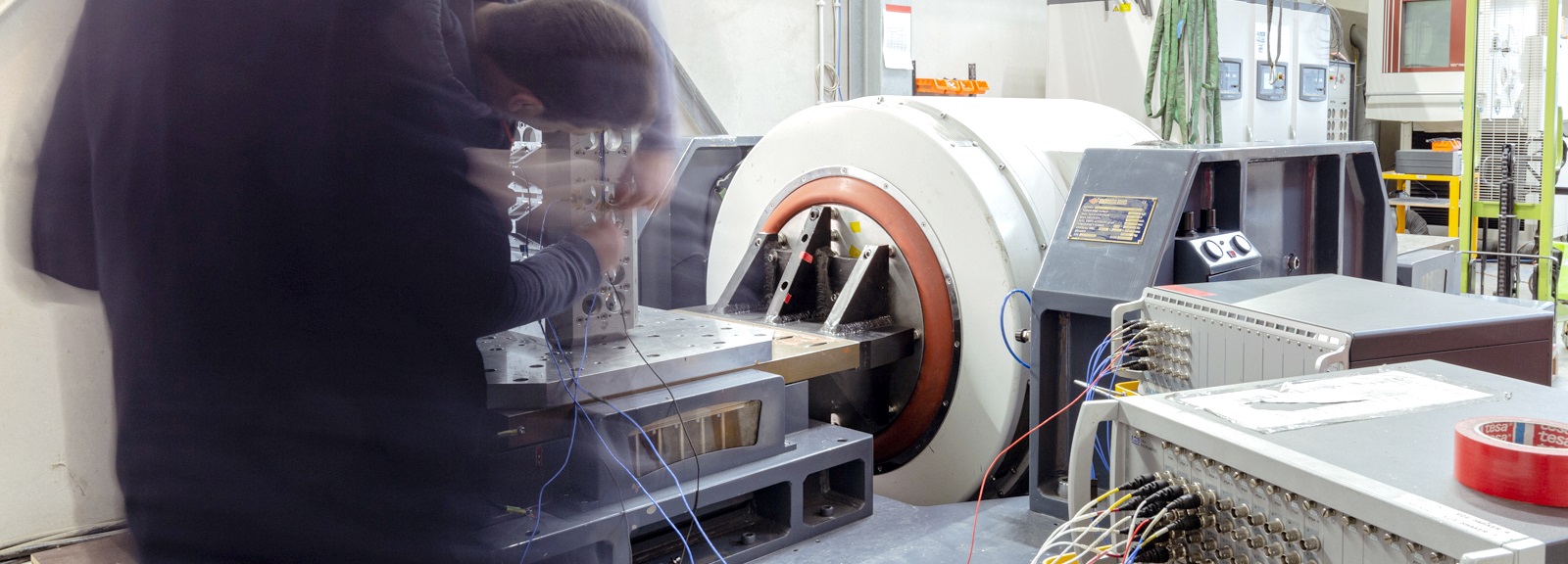
Environmental testing
V2i has a full range of test facilities, some of them unique in their capabilities. Our experienced test staff is able to test small devices or large equipment (up to 1 ton), from very low frequencies (e.g. 0.1 Hz for seismic testing) to very high frequencies (above 20 kHz for ultrasonic applications) for any kind of excitation: sine, random, combined or shocks (Flexible Scope – Detailed Scope).
V2i’s team of experienced field doctors, engineers and technicians provide our partners with customised response for their applications:
- engineering tests that aim to validate the design of a prototype. V2i offers complementary services in defining specs, instrumentation, equipment monitoring during testing or operating deflection shapes (ODS);
- qualification tests according to standards from aeronautics, space, defence, the rail industry and more;
- High Cycle Fatigue testing to determine the endurance limit of a material, a design or to validate a manufacturing process.
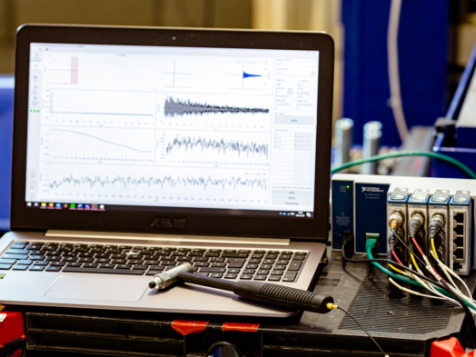
This technique is of great interest when we need to assess the dynamic behaviour of a prototype or to better understand the dynamic response of a piece of equipment being tested or operating in a vibration environment.
Thanks to analysis software tools developed by V2i, experimental modal parameters can be easily correlated to simulation results. Then, if required, V2i’s simulation engineers can suggest structural modifications to ensure safe and reliable in-service running.
Modal Testing
Modal Testing, also referred to as Modal Analysis or Experimental Modal Analysis, makes it possible, through experimentation, to determine the modal parameters of a structure or equipment, i.e. its natural frequencies, modal shapes and modal dampings.
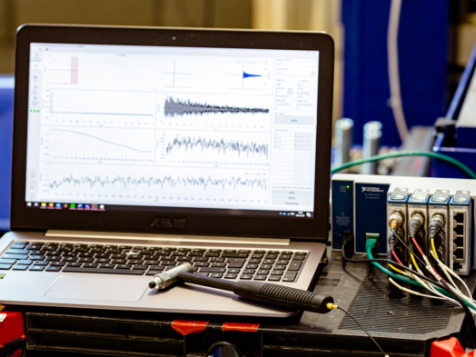
This technique is of great interest when we need to assess the dynamic behaviour of a prototype or to better understand the dynamic response of a piece of equipment being tested or operating in a vibration environment.
Thanks to analysis software tools developed by V2i, experimental modal parameters can be easily correlated to simulation results. Then, if required, V2i’s simulation engineers can suggest structural modifications to ensure safe and reliable in-service running.
Thanks to a team of experts in structural dynamics, and next to classical hammer impact and shaker testing techniques, V2i has developed unique methods to identify the modal parameters of very challenging cases, like civil engineering and cyclically repeating structures from aeronautics. Most of them have led to interesting scientific publications after their industrial applications were validated. They can be downloaded here!
Simulation
V2i provides strong, comprehensive expertise in simulating vibration-related phenomena, thanks to its academic background and its highly qualified team of doctors and engineers.
Here are some of the main applications we are used to dealing with:
- numerical modal analysis
- computation of mechanical stresses due to vibrations (harmonic, random or combined)
- fatigue studies
- rotor dynamics
- and much more!